Glossário Lean Thinking
LEAN: termo de origem inglesa que significa magro, enxuto, algo que contém apenas o que é necessário.
LEAN MANUFACTURING: filosofia que processa a organização de atividades produtivas tendo em vista a eliminação de desperdício e compromisso de melhoria continua de todos os processos operacionais por parte dos colaboradores.
LEAN THINKING: filosofia de gestão através da qual as organizações desenvolvem competências no sentido da gradual eliminação do desperdício e criação de valor.
LEAN PRODUCTION: produção de uma grande variedade de produtos em pequenos lotes e em reduzidos tempos de fabricação, possuem com característica alta qualidade, flexibilidade e baixos custos.
VALOR: aquilo que é entregue ao cliente e que este considera como importante. Refere-se ao nível de satisfação que o cliente experimentou como resultado da entrega que lhe foi feita.
VSM (VALUE STREAM MAPPING): é o mapeamento da cadeia de valor. Trata-se de um método sistemático de identificação de todas as atividades necessárias para produzir um produto ou serviço. O mapeamento também inclui fluxo de materiais e de informação.
6 SIGMA (SIX SIGMA): metodologia que através do uso de dados provenientes do processo, reduz a variação (mura) dos processos de forma sistemática. Baseia-se num conjunto de ferramentas estatísticas e planos para observar e gerir as variáveis criticas dos processos, bem como a relação entre elas. O valor de sigma mede a capacidade do processo se realizar sem erros e aumentar a satisfação do cliente. A unidade é medida em defeitos por milhão e quanto menor melhor será o processo.
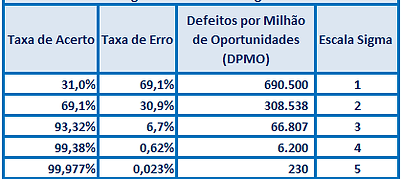
BLACK BELT: líder de equipe em ambiente six sigma que é responsável pela implementação de projetos de melhoria continua na empresa.
MASTER BLACK BELTS: são especialistas em six sigma responsáveis pela implementação estratégica nas organizações. São pessoas no topo da hierarquia six sigma.
GREEN BELT: técnico formado e treinado na metodologia six sigma que é envolvido em processos de melhoria ou em equipes de melhoria da qualidade
MURA: palavra de origem japonesa que significa variação e variedade indesejáveis nos processos de trabalho ou no out-put de um processo.
MUDA: palavra de origem japonesa que significa desperdício ou atividade que consome recursos e não acrescenta valor.
MURI: palavra de origem japonesa que significa excesso, exagero.
AUTONOMAÇÃO (AUTONOMATION ou JIDOKA): transferência de inteligência humana para equipamento automatizado de modo que o equipamento seja capaz de detectar erros e defeitos nos processos e imediatamente param os processos evitando a propagação dos problemas.
KAIZEN: palavra de origem japonesa que significa melhoria continua de processos e de sistemas de trabalho. Pode envolver pessoas e equipamentos.
KANBAN: palavra de origem japonesa que significa cartão. É um dos mais simples sistemas de controle de operações que se conhece e um dos elementos primários do TPS. O sistema Kanban coordena o fluxo de materiais e de informações ao longo do processo de fábrica de acordo com o sistema pull.
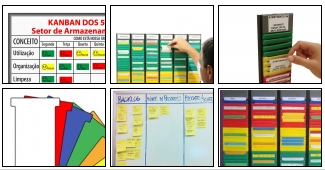
TPS (Toyota Production System): é um sistema de produção desenvolvido pela Toyota entre 1948 e 1975, que aumenta a produtividade e a eficiência, evitando o desperdício, como a de tempo de espera, superprodução, gargalos de transporte e inventário desnecessário. Foi desenvolvido por Taiichi Ohno, sendo que o sistema integra o Lean Manufacturing, Just-in-Time, Kanban e o nivelamento de produção ou Heijunka.
JUST IN TIME (JIT): sistema de produção repetitiva no qual o processamento e movimentação de materiais ocorrem a medida que estes são necessários e usualmente em pequenos lotes.
SISTEMA PULL: é um dos três sistemas do JIT. Trata-se de um sistema de fábrica coordenado pelo cliente. As atividades de fábrica iniciam-se apenas na presença de um pedido ou ordem do cliente.
SISTEMA PUSH: é o sistema clássico de gestão da produção que se caracteriza por empurrar os produtos da empresa para o cliente. Caracterizado por previsões de mercado e controles internos rígidos e nada orientados ao mercado.
MILK RUN: veiculo de transporte de materiais, interno ou externo, que faz o abastecimento ponto a ponto de acordo com as necessidades Just in Time. É também um método de disciplinar o fluxo de materiais evitando falhas e excessos.
ANDON: dispositivo de controle visual utilizado para fazer o controle de processos de trabalho e produção informando os colaboradores do status do mesmo. Pode ser elétrico ou eletrônico e também pode ser utilizado para alertar sobre problemas ou intervenções.

LEAD TIME: tempo necessário para realizar uma dada tarefa, trabalho, produto ou serviço. É um tempo composto pelo tempo útil de processamento e também pelo tempo não produtivo para armazenamento, transportes ou setups.
TAKT TIME: é um tempo de ciclo definido de acordo com a procura ou demanda. Se a procura aumentar o Takt Time deve diminuir e vice-versa.
POKA YOKE: expressão japonesa que significa “a prova de erros”.
CEP: Controle Estatístico do Processo.
LAYOUT: arranjo físico dos recursos num determinado espaço de trabalho. Existem vários tipos de acordo com diferentes estratégias de produção e processos produtivos.
KPI(KEY PERFORMANCE INDICATOR): métricas estratégicas para medir e mensurar resultados. Está associado ao BSC – Balanced Scored Card.
OEE (OVERALL EQUIPAMENT EFFICIENCY): Eficiência Global do Equipamento é uma métrica que avalia o desempenho global do sistema de operações ao considerar os 3 elementos envolvidos na criação de valor, ou seja: pessoas, processos e tecnologia. Para cálculo do OEE são considerados os fatores de Qualidade, Performance e Disponibilidade.

TMP (TOTAL PRODUCTIVE MAINTENANCE): Manutenção Produtiva Total é um sistema desenvolvido no Japão a fim de eliminar perdas nas máquinas, perda nos métodos, perda de matéria-prima, perdas de energia, reduzir paradas, garantir a qualidade e diminuir custos nas empresas com processos contínuos. O TPM gera ordens de intervenção programadas e mantém um histórico de reparações e operações realizadas em determinado equipamento.
MAPA SIPOC (Suppliers, Inputs, Process, Outputs, Customers): é uma ferramenta usada por uma equipe para identificar todos os elementos relevantes de um projeto de melhoria de processo antes do início do trabalho. Ele ajuda a definir um projeto complexo que ainda não possui um escopo bem conhecido, e é normalmente utilizado na fase de Medição da metodologia Six Sigma DMAIC (Definir, Medir, Analisar, Melhorar, Controlar). Ele é similar e está relacionado ao mapeamento de processos, mas fornece detalhes adicionais.

DMAIC: é um método de resolução de problemas dividido em cinco etapas: Define (Definir), Measure (Medir), Analyze (Analisar), Improve (Melhorar) e Control (Controlar). Começou a ser difundido pela Motorola na década de 80 do século passado e foi massificado pela GE dentro do Programa Seis Sigma que forma especialistas conhecidos como Black e Green Belts que são empenhados em atacar problemas de maneira organizada, e com apoio de ferramentas de qualidade e estatísticas mais complexas.

CICLO PDCA: trata do planejamento (PLAN) da atividade ou tarefa, da sua execução (DO), da comparação dos resultados com os padrões previamente estabelecidos (CHECK) e da implementação (ACT) de ações de melhoria (ou ações corretivas), sempre que forem observados desvios.
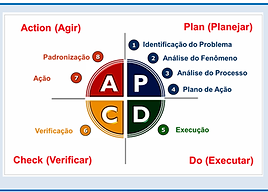
5´S: Filosofia japonesa que enfatiza o conceito de manter em ordem o local de trabalho, propiciando eficiência, melhores condições de trabalho e eliminação de desperdícios. Seiri - Senso de Utilização; Seiton - Senso de Ordenação; Seiso - Senso de Limpeza; Seiketsu - Senso de Higiene e Asseio; Shitsuke - Senso de Disciplina.
DOWNSIZING: Redução dos níveis hierárquicos numa organização para aproximar a alta administração dos níveis operacionais, propiciando uma comunicação mais eficaz, melhor delegação de poder e agilização nas tomadas de decisão.
BENCHMARKING: avaliação e comparação do desempenho ou perfil de uma organização com organizações similares que são consideradas as melhores na sua classe ou atividade. Implementar melhores práticas de uma organização em outra.
FLUXOGRAMA: Diagrama que representa o fluxo ou sequência atual de um trabalho ou processo de produção de um produto ou serviço, por meio de simbologia própria. O fluxograma documenta um processo de produção ou seqüência de atividades desempenhadas por um indivíduo, setor, departamento ou organização, não importando o nível de complexidade e é muito útil por permitir uma boa compreensão do conjunto, e possibilitar a fixação dos limites de cada atividade, processo ou da organização. O fluxograma deve apresentar a realidade atual e não situações ideais ou pressuposições.
.

FOLHA DE PROCESSO: Documento que estabelece a seqüência de operações a serem realizadas para a produção ou fabricação de um material, item ou produto, montagem de um conjunto ou prestação de um serviço. Uma folha de processo pode ser completa, por exemplo, envolvendo desde a preparação das matérias-primas e insumos até a estocagem ou expedição, ou dividida, referente a cada processo específico.
FOLHA DE VERIFICAÇÃO: Formulário no qual um conjunto de dados pode ser sistematicamente coletado e registrado de maneira ordenada e uniforme, permitindo rápida interpretação de resultados. Utilizada para coleta de dados visando identificar e quantificar problemas ou oportunidades de melhoria. Ajuda a transformar "opiniões" em "fatos". É uma das sete ferramentas do controle da qualidade.
FOLLOW-UP: Processo de monitoração do estado real da qualidade de modo a possibilitar o cumprimento de objetivos e metas, e a detecção da necessidade de ações corretivas.
DIAGRAMA DE ISHIKAWA: também conhecido como Diagrama de Causa e Efeito ou Espinha de Peixe permite estruturar hierarquicamente as causas de determinado problema ou oportunidade de melhoria. Serve para que todos os envolvidos na solução de um processo industrial consigam visualizar melhor o efeito indesejado ocorrido e as suas possíveis causas. As causas de um problema podem ser agrupadas, a partir do conceito dos 6M, como decorrentes de falhas em: materiais, métodos, mão-de-obra, máquinas, meio ambiente, medidas.
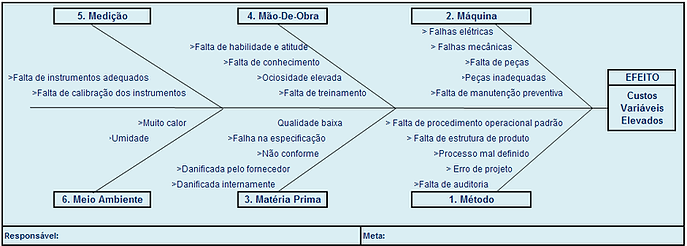
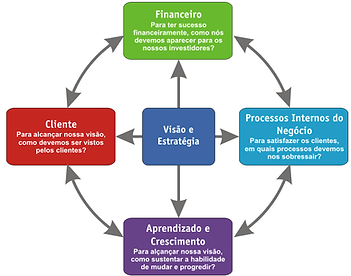
BALANCED SCORECARD: é uma metodologia de medição e gestão de desempenho. O Balanced Scorecard reflete o equilíbrio entre os objetivos de curto e longo prazo, medidas financeiras e não-financeiras, indicadores de tendências e ocorrências e também entre as perspectivas interna e externa de desempenho. Este conjunto abrangente de medidas serve de base para o sistema de medição e gestão estratégica por meio do qual o desempenho organizacional é mensurado de maneira equilibrada sob as quatro perspectivas. Dessa forma contribui para que as empresas acompanhem o desempenho financeiro, monitorando, ao mesmo tempo, o progresso na construção de capacidades e na aquisição dos ativos intangíveis necessários para o crescimento futuro.
EMPOWERMENT: é uma abordagem a projetos de trabalho que se baseia na delegação de poderes de decisão, autonomia e participação dos funcionários na administração das empresas. Analisa-se o desenvolvimento, ou grau de maturidade, do empoderamento na organização avaliando o estágio evolutivo em que se encontram as áreas de gestão, as configurações organizacionais, as estratégias competitivas, a gestão de recursos humanos e a qualidade
ERP (Enterprise Resources Planning): Sistema integrado de gestão empresarial é um sistema de informação que integra todos os dados e processos de uma organização em um único sistema. A integração pode ser vista sob a perspectiva funcional (sistemas de finanças, contabilidade, recursos humanos, fabricação, marketing, vendas, compras) e sob a perspectiva sistêmica (sistema de processamento de transações, sistemas de informações gerenciais, sistemas de apoio a decisão)
FMEA: é a Análise do modo e efeito de falha, é um estudo sistemático e estruturado das falhas potenciais que podem ocorrer em qualquer parte de um sistema para determinar o efeito provável de cada uma sobre todas as outras peças do sistema e no provável sucesso operacional, tendo como objetivo melhoramentos no projeto, produto e desenvolvimento do processo.
ESTRANGULAMETO (BOTTLENECK): qualquer recurso interno ou externo que crie estrangulamento ou dificuldade ao normal funcionamento de um sistema ou gargalos no processo. Trata-se de uma limitação ou constrangimento.
CADEIA DE VALOR: sequencia de atividades e operações envolvidas na criação e entrega de um produto ou serviço.
GEMBA: palavra Japonesa para “local de trabalho” (Planta fabril ou shop floor). Significa melhoria continua no lugar de trabalho.
GRÁFICO DE GANTT: um gráfico de controle desenhado para o acompanhamento e execução dos planos de trabalho, produção e projetos. Foi desenvolvido por Henry Gantt ( 1861-1919) no inicio do século XX.
HISTOGRAMA: ferramenta de análise de problemas que graficamente apresenta dados de uma distribuição. Gráfico de barras verticais.

GRÁFICO DE PARETO: é a apresentação de dados por ordem de tamanho, importância ou prioridade, favorecendo a tomada de decisões pela facilidade com que se reconhecem quais são as causas principais. Com Base no princípio de Pareto (80% dos problemas advém de 20% das causas) pode-se coletar dados sobre refugo, defeitos, desperdícios ou qualquer outro problema que necessite ser analisado e apresentá-lo de maneira com que se possa estabelecer prioridades.

DIAGRAMA DE DISPERSÃO: é utilizado para estudar a possível relação entre duas variáveis. Dessa forma, o diagrama de dispersão é usado para se verificar uma possível relação de causa e efeito. Isto não prova que uma variável afeta a outra, mas torna claro se a relação existe e em que intensidade. O diagrama de dispersão é construído de forma que o eixo horizontal represente os valores medidos de uma variável e o eixo vertical represente as medições da segunda variável.

GRAFICO DE TENDÊNCIA: utilizado para apresentar séries cronológicas, por exemplo, oscilações na quantidade de refugo produzido em um determinado período. Pode-se verificar, por exemplo, através deste gráfico, se uma ação corretiva está apresentando o resultado esperado.
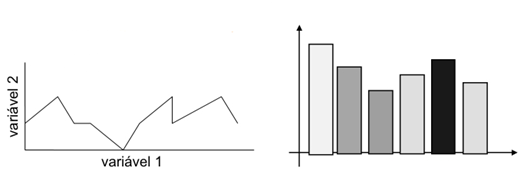